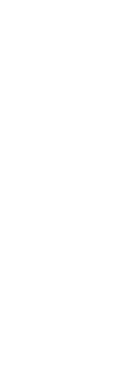
Aluminium composite panels (ACPs) give designers and architects a versatile and resilient facade solution, but care must be taken to ensure that high standards are applied. Angelos Zografos, technical sales engineer at Elval Colour, explains the quality considerations that go into the production of ACPs and why manufacturers should make the welfare of employees and the environment a priority.
Aluminium composite panels (ACPs) offer architects a supreme and versatile material for building facades. The panels demonstrate a rigidity that is often not available in solid metal surfaces, and this prevents the material from deforming due to local buckling, a result known as oil canning. This provides an extremely flat surface onto which high-specification liquid coil coatings can be applied, allowing the panels to resist oxidisation and degradation even in extreme environments. At the same time, a limitless variety of colour coatings enables greater flexibility and freedom in aesthetic design, an important parameter for materials used in the hospitality sector. In addition, ACPs are lighter than alternative materials, such as solid aluminium; this makes them ideal for renovating existing facilities as it allows a visual and functional upgrade of the facade without requiring major modifications of the existing structure.
Furthermore, when produced with a core of special composition, it can also be fire-retardant or even incombustible. This attribute is of paramount importance in today’s world, where fire safety becomes more important every day – particularly for facilities of high occupancy or visitation, such as hotels, schools or hospitals. However, the complex process for the production of ACPs means that strict attention must be paid to ensure quality is maintained.
This is a key priority for the aluminium coil coater and ACP producer Elval Colour, which offers three varieties of ACPs: etalbond, etalbond FR (fire-retardant) and etalbond A2 (incombustible). Elval Colour opts for manufacturing at the highest possible level. “The most important factor is to be consistent through the whole year, with no deviations regarding our production quality,” emphasises Angelos Zografos. He adds that the company’s practice in coil coating and producing ACPs is certified and rigorously audited by independent certification bodies and demonstrates a long record of reliability.
ACPs are comprised of a lightweight organic core with mineral fillers and two coil-coated aluminium sheets, between which the core is sandwiched and bonded with adhesive. Aluminium oxidises, therefore it needs to be treated accordingly; the process of rolling, which is the transformation of an aluminium slab into a coil, results in oxidisation as well as contamination of the aluminium surface from the lubricants and other agents that are used to facilitate the procedure. Thus, it is a key step to clean the aluminium surface by chemically treating it with a combination of alkaline and acidic washing to remove the smut and any oxides from it. After that, a passivation layer is applied, which restricts future oxidisation of the surface and is polarised enough to bond with the coating that is added next. This pretreatment is vital: if omitted or done incorrectly, it will allow reactivity of the surface, which leads to corrosion. “This kind of pretreatment is not done in some cases,” says Zografos. “This creates the basis for the future oxidisation of the aluminium substrate.”
Finally, the coating is applied; it is typically a polyvinylidene fluoride (PVDF) coating that provides protection against the elements and gives the aesthetic qualities of ACPs. However, the quality of this coating can vary. The normal composition is 70% PVDF and 30% acrylic, but as Zografos adds, “If the PVDF content goes lower, the quality and the cost drop dramatically.” The coatings used by Elval Colour have an 80% PVDF content and contain no hazardous substances, such as lead, chrome or isophorone.
Additionally, as hospitality establishments can often be located in areas with conditions that are aggressive for coatings – such as next to the sea or in an area with increased UV radiation – a more advanced coating solution might have to be applied to the ACPs, which could mean more layers or even different technology. The details of that coating solution have to be agreed along with the client as they will support the warranty that will accompany the material, and it will protect the image and the value of the facility in the long run. Badly defined warranties and unsuitable coating solutions can undermine the quality and value of the project.
This commitment to quality extends to the behaviour of ACPs against fire. Elval Colour’s etalbond A2 is classified as A2-s1,d0 according to the European standard EN 13501-1 and will not contribute to a fire, making it an ideal facade solution for tall buildings and high-occupancy facilities, such as hotels or convention centres. In addition, the panels will not emit toxic chemicals when exposed to the fire, which could harm occupants.
Furthermore, hydroxides found in the core give it fire-retardant properties by evaporating when heated, causing an endothermic reaction and a reduction in temperature. “You have a similar performance as the solid material, which cannot catch fire,” Zografos states. “The industry saw that there was a need for improvement, to move forward and advance from the standard that was available several years ago with the plastic core.”
Elval Colour is strongly committed to sustainability. “You might have really beautiful and useful products, but, as an architect, you should not only see what lies in front of you, but you should also care about what is happening backstage,” Zografos explains. “The production of building materials is strongly connected to the environment, so we have to be careful what we release and how.” Elval Colour uses an afterburner and thermal oxidisers in its coating process, which burn all the solvents that evaporate from the coating. This process not only prevents harmful volatile organic compounds from being released into the atmosphere but also redirects the generated heat back in the furnace, which cures the coatings, therefore saving energy and making the liquid coating process even more environmentally friendly. Water used in the process is entirely reused, and the product – etalbond ACP – is fully recyclable.
Zografos also stresses that a good working environment plays a key role in ensuring a high-quality product. “A safe working environment will add to the quality of the product because people are a crucial factor in the whole production chain,” he says. The focus on this principle is evident from Elval Colour’s OHSAS 18001 certification for occupational health and safety.
All these factors lead to the creation of a product that fulfils the highest specifications and is also suitable for a wide range of environments and architectural needs. Continuous and close collaboration with architects and designers throughout the years allows Elval Colour to maintain a profound understanding of market needs and thus, if the need arises, be able to produce tailor-made solutions with a high level of customisation.
In Tenerife, Spain, the facade of the Hard Rock Cafe Hotel consists of 16,000m² of etalbond acp in 16 different colours, specially customised to withstand the harsh environmental effects, such as salt water and rain, resulting from the buildings proximity to the sea. Zografos concludes that, “The hospitality sector can benefit from the versatility of the personalised solutions that we offer and the value we add to their services through products of quality, like etalbond.”
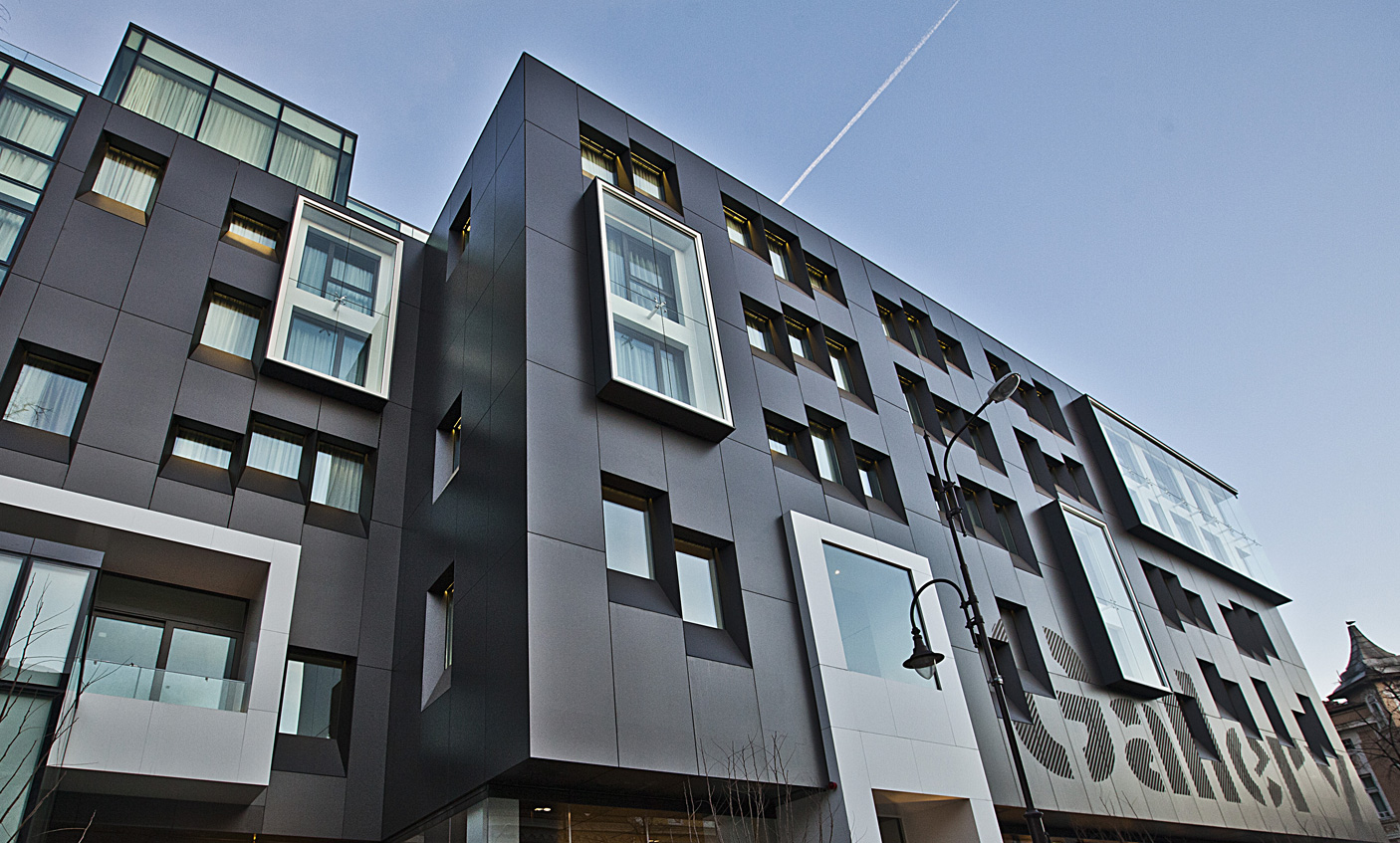
Aluminium composite panels (ACPs) give designers and architects a versatile and resilient facade solution, but care must be taken to ensure that high standards are applied. Angelos Zografos, technical sales engineer at Elval Colour, explains the quality considerations that go into the production of ACPs and why manufacturers should make the welfare of employees and the environment a priority.
Aluminium composite panels (ACPs) offer architects a supreme and versatile material for building facades. The panels demonstrate a rigidity that is often not available in solid metal surfaces, and this prevents the material from deforming due to local buckling, a result known as oil canning. This provides an extremely flat surface onto which high-specification liquid coil coatings can be applied, allowing the panels to resist oxidisation and degradation even in extreme environments. At the same time, a limitless variety of colour coatings enables greater flexibility and freedom in aesthetic design, an important parameter for materials used in the hospitality sector. In addition, ACPs are lighter than alternative materials, such as solid aluminium; this makes them ideal for renovating existing facilities as it allows a visual and functional upgrade of the facade without requiring major modifications of the existing structure.
Furthermore, when produced with a core of special composition, it can also be fire-retardant or even incombustible. This attribute is of paramount importance in today’s world, where fire safety becomes more important every day – particularly for facilities of high occupancy or visitation, such as hotels, schools or hospitals. However, the complex process for the production of ACPs means that strict attention must be paid to ensure quality is maintained.
This is a key priority for the aluminium coil coater and ACP producer Elval Colour, which offers three varieties of ACPs: etalbond, etalbond FR (fire-retardant) and etalbond A2 (incombustible). Elval Colour opts for manufacturing at the highest possible level. “The most important factor is to be consistent through the whole year, with no deviations regarding our production quality,” emphasises Angelos Zografos. He adds that the company’s practice in coil coating and producing ACPs is certified and rigorously audited by independent certification bodies and demonstrates a long record of reliability.
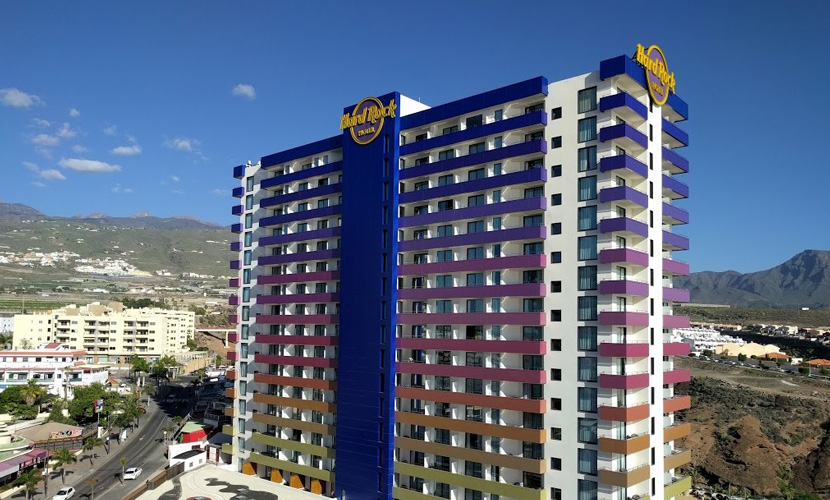
ACPs are comprised of a lightweight organic core with mineral fillers and two coil-coated aluminium sheets, between which the core is sandwiched and bonded with adhesive. Aluminium oxidises, therefore it needs to be treated accordingly; the process of rolling, which is the transformation of an aluminium slab into a coil, results in oxidisation as well as contamination of the aluminium surface from the lubricants and other agents that are used to facilitate the procedure. Thus, it is a key step to clean the aluminium surface by chemically treating it with a combination of alkaline and acidic washing to remove the smut and any oxides from it. After that, a passivation layer is applied, which restricts future oxidisation of the surface and is polarised enough to bond with the coating that is added next. This pretreatment is vital: if
omitted or done incorrectly, it will allow reactivity of the surface, which leads to corrosion. “This kind of pretreatment is not done in some cases,” says Zografos. “This creates the basis for the future oxidisation of the aluminium substrate.”
Finally, the coating is applied; it is typically a polyvinylidene fluoride (PVDF) coating that provides protection against the elements and gives the aesthetic qualities of ACPs. However, the quality of this coating can vary. The normal composition is 70% PVDF and 30% acrylic, but as Zografos adds, “If the PVDF content goes lower, the quality and the cost drop dramatically.” The coatings used by Elval Colour have an 80% PVDF content and contain no hazardous substances, such as lead, chrome or isophorone.
Additionally, as hospitality establishments can often be located in areas with conditions that are aggressive for coatings – such as next to the sea or in an area with increased UV radiation – a more advanced coating solution might have to be applied to the ACPs, which could mean more layers or even different technology. The details of that coating solution have to be agreed along with the client as they will support the warranty that will accompany the material, and it will protect the image and the value of the facility in the long run. Badly defined warranties and unsuitable coating solutions can undermine the quality and value of the project.
This commitment to quality extends to the behaviour of ACPs against fire. Elval Colour’s etalbond A2 is classified as A2-s1,d0 according to the European standard EN 13501-1 and will not contribute to a fire, making it an ideal facade solution for tall buildings and high-occupancy facilities, such as hotels or convention centres. In addition, the panels will not emit toxic chemicals when exposed to the fire, which could harm occupants.
Furthermore, hydroxides found in the core give it fire-retardant properties by evaporating when heated, causing an endothermic reaction and a reduction in temperature. “You have a similar performance as the solid material, which cannot catch fire,” Zografos states. “The industry saw that there was a need for improvement, to move forward and advance from the standard that was available several years ago with the plastic core.”
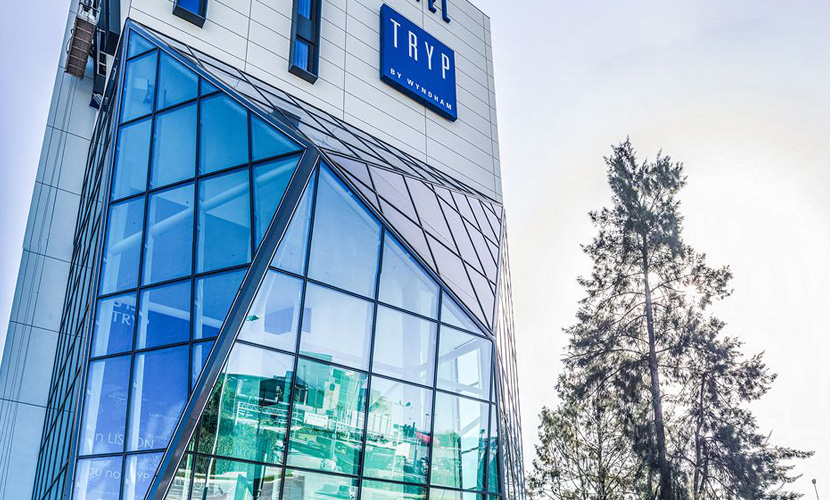
Elval Colour is strongly committed to sustainability. “You might have really beautiful and useful products, but, as an architect, you should not only see what lies in front of you, but you should also care about what is happening backstage,” Zografos explains. “The production of building materials is strongly connected to the environment, so we have to be careful what we release and how.” Elval Colour uses an afterburner and thermal oxidisers in its coating process, which burn all the solvents that evaporate from the coating. This process not only prevents harmful volatile organic compounds from being released into the atmosphere but also redirects the generated heat back in the furnace, which cures the coatings, therefore saving energy and making the liquid coating process even more environmentally friendly. Water used in the process is entirely reused, and the product – etalbond ACP – is fully recyclable.
Zografos also stresses that a good working environment plays a key role in ensuring a high-quality product. “A safe working environment will add to the quality of the product because people are a crucial factor in the whole production chain,” he says. The focus on this principle is evident from Elval Colour’s OHSAS 18001 certification for occupational health and safety.
All these factors lead to the creation of a product that fulfils the highest specifications and is also suitable for a wide range of environments and architectural needs. Continuous and close collaboration with architects and designers throughout the years allows Elval Colour to maintain a profound understanding of market needs and thus, if the need arises, be able to produce tailor-made solutions with a high level of customisation.
In Tenerife, Spain, the facade of the Hard Rock Cafe Hotel consists of 16,000m² of etalbond acp in 16 different colours, specially customised to withstand the harsh environmental effects, such as salt water and rain, resulting from the buildings proximity to the sea. Zografos concludes that, “The hospitality sector can benefit from the versatility of the personalised solutions that we offer and the value we add to their services through products of quality, like etalbond.”