Technology
Print big: exploring the future of 3D printing in architecture with Aectual
Dutch architecture company Aectual has launched a digital 3D printing platform that allows architects and designers to create customised finishing and furniture products. Luke Christou speaks to CEO Hans Vermeulen to find out more about the platform and the future of 3D printing in architecture.
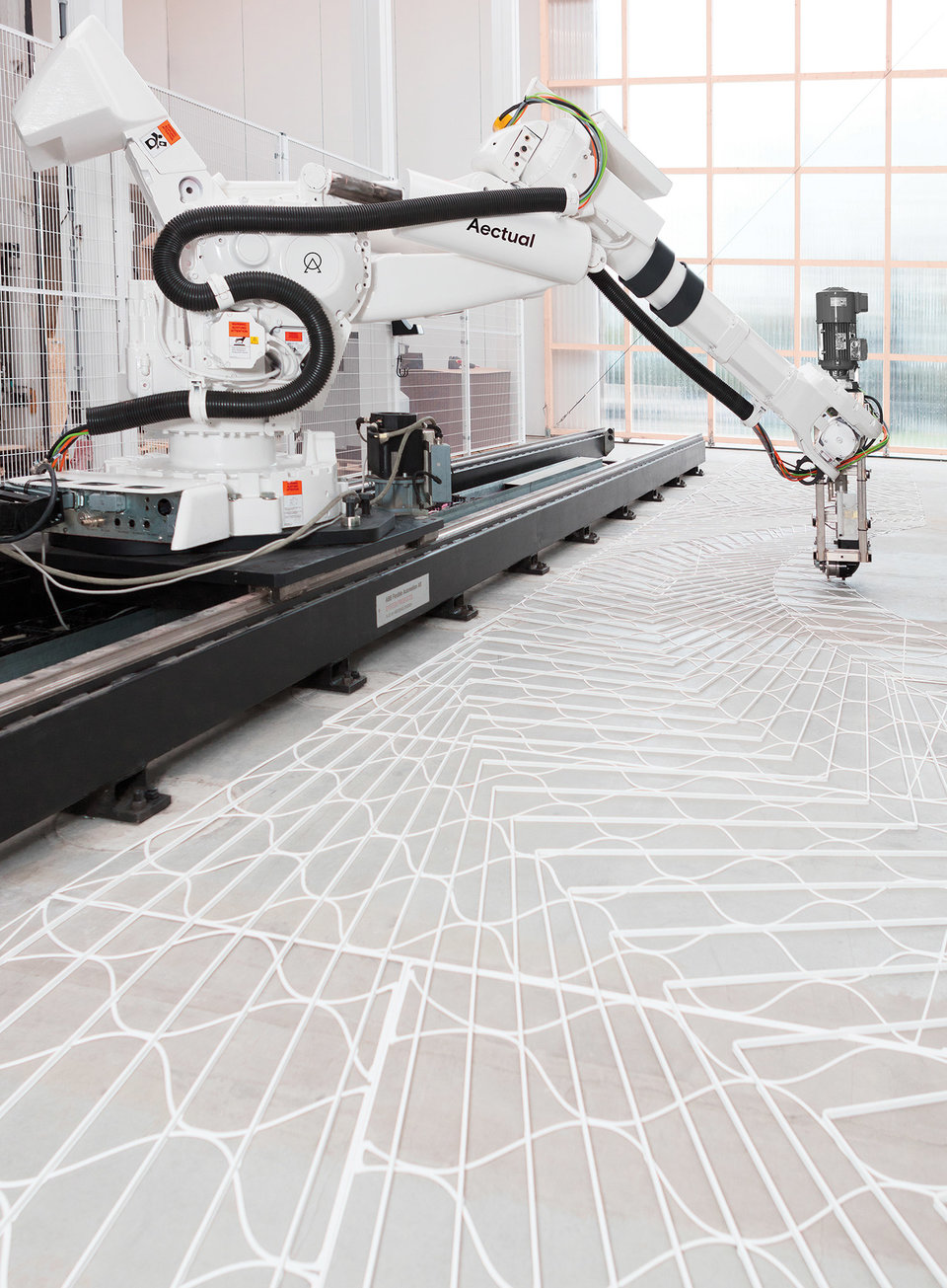
E
arlier this year, design technology firm Aectual announced the global beta launch of its design-to-delivery platform. The intuitive platform enables designers to create and customise products not only for their projects and clients, but to bring these products to a wider audience, who can in turn customise the product to their space.
“Designers can create their own designs for their own projects, but they can also bring their designs to a way wider audience than normally architecture has,” says Hans Vermeulen, CEO and co-founder of Aectual.
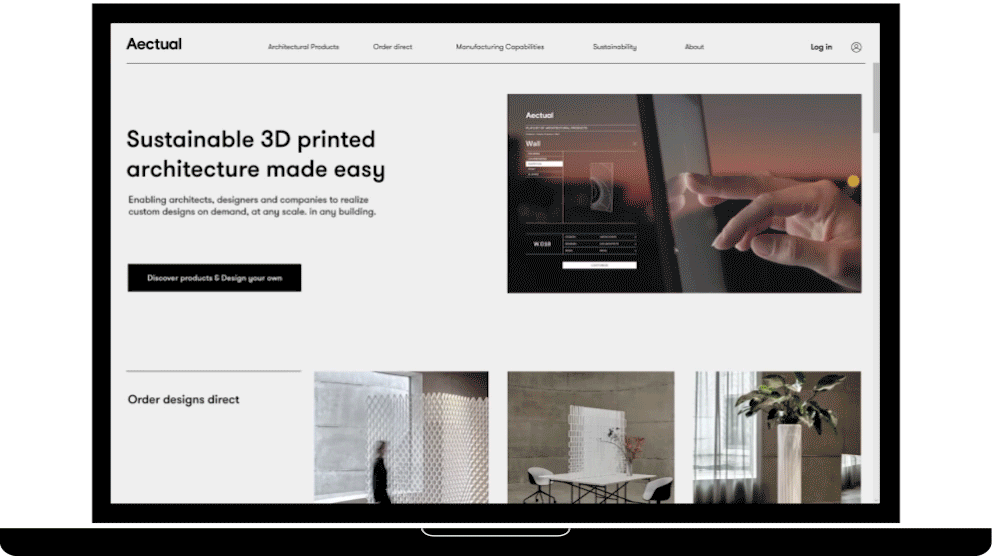
Aectual’s platform lets architects and designers to create, customise and 3D print products. Credit (all images): Aectual
Designed to fit
Currently, Aectual offers 17 items for customers to order. With no two buildings the same, each product can be tweaked within the platform to fit a space and meet the customer’s specific needs, providing a seamless way to produce custom designs at any scale.
While customisation is different for each product, options may include dimensions, shape, material, colour and finish. For specific products, the user can use Aectual’s guidelines to create a design using their own preferred software and upload it to the platform.
Through a partnership with Arup, experts are on hand to assist with the engineering aspect of particularly tricky products and designs.
There are times when users may push their designs beyond what Aectualrefers to as the ‘possibility space’ for the product. However, through its partnership with Arup, experts are on hand to assist with the engineering aspect of particularly tricky products and designs, such as its staircases, which can take ‘virtually any shape’.
Once a design is saved, it is added to the user’s personal dashboard, where they are guided through the various production decisions, from thickness to mounting systems, that they must make before finalising the design.
“In that dashboard, you can constantly change those parameters as a designer, based on your clients’ wishes or budget, until the moment you confirm,” Vermeulen says.
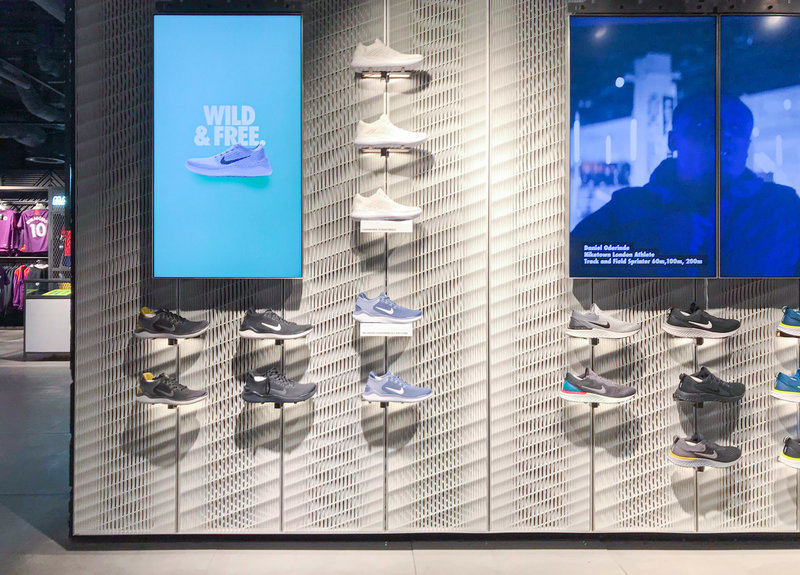
A 3D printed weave panel wall installed at Nike Town London. Aectual enables corporate customers to produce custom interiors.
Bringing digital design files to life
Once confirmed, print files are generated and transferred via the cloud to Aectual’s Amsterdam production facility, ready to be printed using the firm’s XL 3D printing technology.
Developed in-house, the system combines a high-capacity industrial extruder with controller technology from ABB Robotics and Siemens. With a print bed of up to 400 square feet, Aectual’s technology offers a complete solution for large-scale 3D printing.
As designs are digitally produced, leaving little opportunity for error, and manufacturing is largely automated, Aectual estimates that its process is already twice as fast as traditional custom production processes. While lead time is dependent on the volume of the order, the process usually takes four to six weeks from confirming the order to installation on site.
“And, in the end, at less cost,” Vermeulen points out. “Not only the production cost, but because you can reduce the installation time because it’s made to measure, so it always fits.”
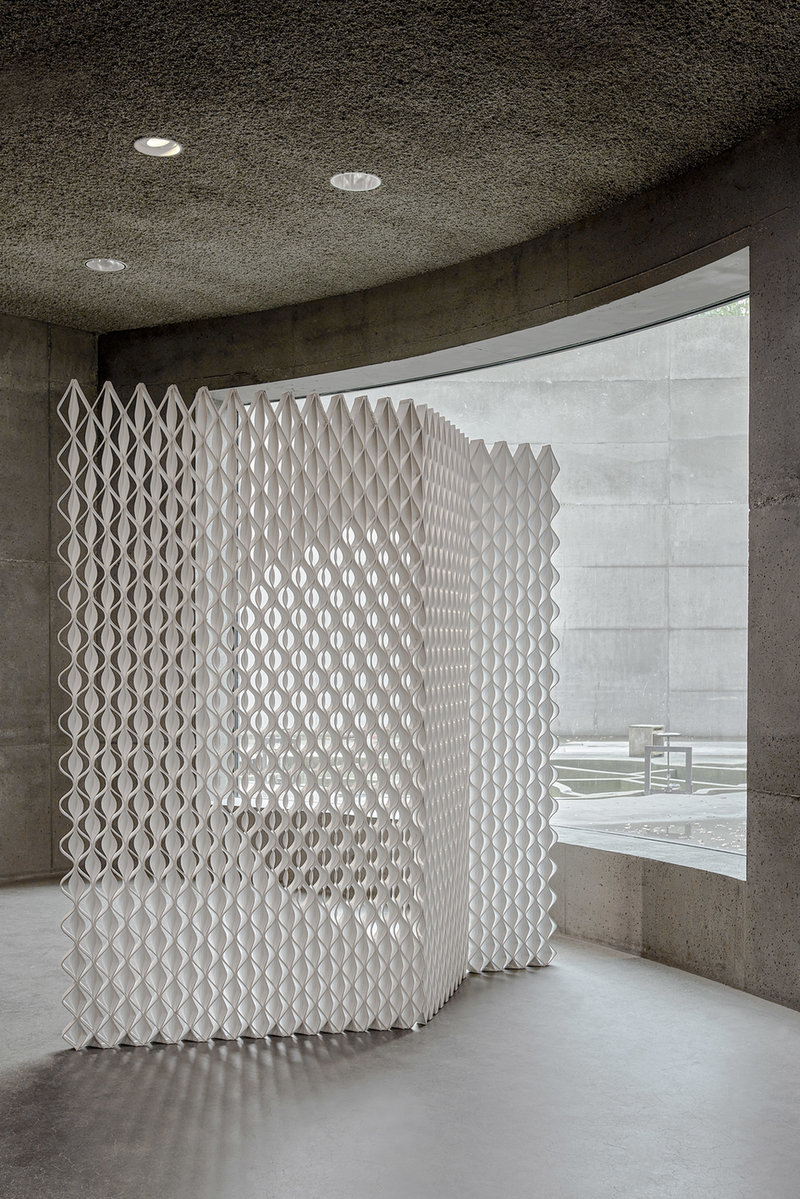
Aectual currently focuses on finishes and furniture, but the technology has potential for 3D printing entire buildings.
Sustainable architecture
Making it easier, faster and cheaper for designers, architects and companies to produce custom products also has significant sustainability benefits. The modification of standardised products is typically to blame for 25% of the waste produced during the fitting process. This issue is eliminated when all products arrive ready to fit.
Sustainability is a key part of Aectual’s mission, and for good reason. A past survey carried out by GloalData’s Construction Intelligence Center found that while 62% of AEC professionals felt sustainable methods increased the cost of completing a project, 85% believe that the industry should still implement such methods.
“Cost, of course, is very important, but sustainability is becoming almost as important,” Vermeulen explains. “Often the AEC industry is said to be lagging behind other industries in all kinds of ways, especially digitalisation. But on sustainability, there’s systems being implemented, from BREEAM to LEED, and that makes products like ours safer, and more favourable for clients to use.”
For its 3D printed items, the company uses a bioplastic that it developed alongside chemical and consumer goods firm Henkel.
Aectual’s products are designed to only use material where it is necessary, reducing material use by up to 70%. As well as its efficient production process, Aectualtries to increase sustainability through the materials it uses.
For its 3D printed items, the company uses a bioplastic that it developed alongside chemical and consumer goods firm Henkel. The polyamide compound is based on renewable resources that is free from environmentally harmful elements. This means that Aectual’s products are less likely to clog up landfills than interiors made from traditional materials.
“The average lifespan of a commercial interior is around three to five years,” Vermeulen says. “While construction is often standing for 50 or more years, interiors are being redone over and over again — and it all goes to waste,”
By using bioplastic, Aectual can provide a circular solution to its customers, who are offered discounts on their next transaction if the material is returned once the interiors reach end of use. The material can then be shredded and reprinted as a new item.
Currently, Aectual can shred and reuse its bioplastic up to seven times. However, it continues to work with Henkel to improve the material.
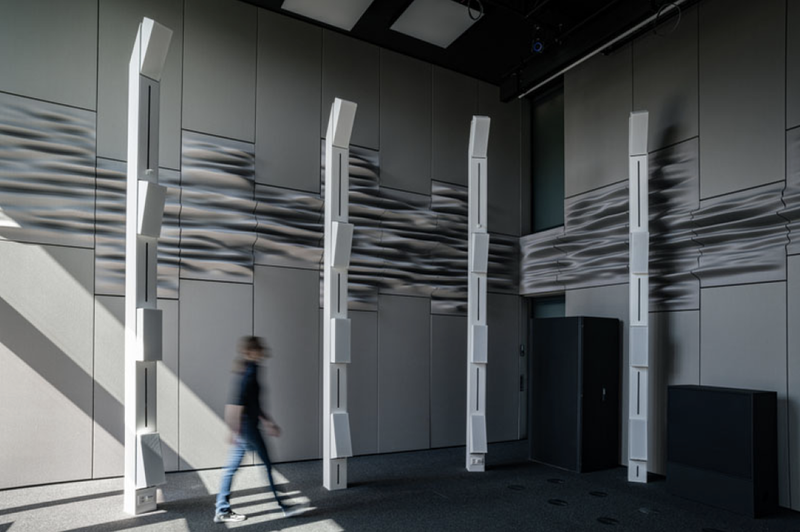
An acoustic panel system designed by Gramazio Kohler Architects is one of the latest designs to join Aectual’s product range.
The 3D printed building
According to the United Nations, three billion people will need better housing by 2030, which will require 96,000 new homes to be built each day. 3D printed housing is often suggested as a solution to the global housing crisis, and many are exploring this potential.
Just recently in Eindhoven, the Netherlands, two occupants became the first in Europe to take up residence in a 3D-printed home, for instance.
Aectualcan create such structures. It’s XL printer is based on technology originally developed by DUS Architects, an architecture firm founded by Aectual’s three co-founders, and was used as part of the firm’s trend-setting 3D Print Canal House project back in 2015.
However, for the time being, Aectual’s focus is on finishing and furniture products. Rather than 3D printing ‘everything’, the company’s goal is to provide a smart way to connect with other methods of building.
“Methods of building in the US are a little different from methods in India,” Vermeulen explains. “For us, it’s important that with tool sets and our parametric products, we fit all building methods and all spaces.”
Rather than 3D printing ‘everything’, the company’s goal is to provide a smart way to connect with other methods of building.
Vermeulen points out that users can already essentially create entire buildings using the platform, though. “If you combine multiple products, you can create a whole space,” he explains. “And if you combine multiple spaces, you have a building”.
Soon, those spaces will become even more customised and complex, as Aectual continues to add new smart products to its range.
Most recently, an acoustic panel system designed by Gramazio Kohler Architects was added to Aectual’s 3D printing platform, which offers acoustically performative designed wall panels with spatial and sound-aesthetics properties. Also joining the growing collection are large scale planters designed by DUS Architects and made from recycled waste plastics.
Main image: Aectual’s XL 3D printing robot has a print bed of up to 400 square feet.