Bricks
From the waste up: building a circular economy for low-carbon bricks
A Heriot-Watt University spin-out has developed a brick made from construction waste which produces only a tenth of the CO2 emissions of a traditional fired brick. Kenoteq co-founder Gabriela Medero explains the potential of a circular economy for bricks in the UK.
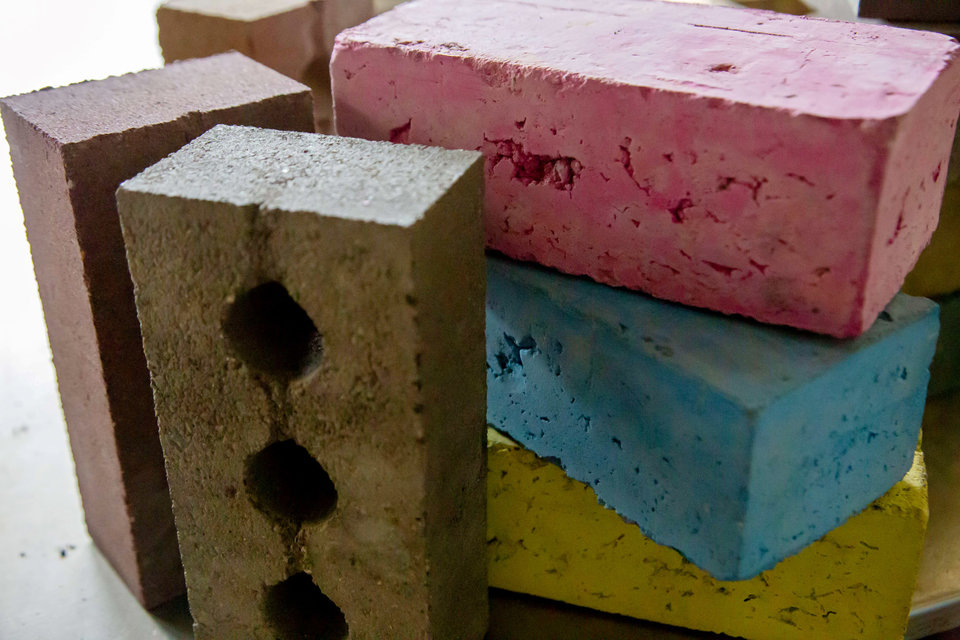
O
ur built environment has significantly impacted the natural environment. It contributes to around 45% of the UK’s overall carbon footprint and was high on the recent COP26 conference agenda with a full day dedicated to addressing its challenges.
While much of the energy expended by the built environment is from the methods we use to heat and cool our buildings, or from other essential utilities like lighting, the materials we use in construction also play a major role. Until recently, these have been regularly overlooked when considering how we can effectively meet our net zero goals.
While planning and design tools have made the technological advances we might expect, becoming increasingly sophisticated in recent years, many of the raw design materials most readily available to architects and building engineers have not kept pace.
As an example, the bricks we use today in most construction projects are still made using largely historic and traditional methods that our ancestors far back in history would recognise – and these methods have tremendous environmental impact.
Félicie Krikler, director at Assael Architecture
Félicie Krikler, director at Assael Architecture
Addressing the environmental footprint of building materials
The energy required to produce a simple clay brick is immense. Fossil fuels are burned to ensure kiln temperatures reach in excess of 1,000°C. This process generates both carbon monoxide and sulphur oxides, and the fine dust created during production adds a further layer of pollution to our air.
Material availability is another concern. As well as draining precious natural resources which are in increasingly short supply, we don’t make enough bricks domestically to meet requirements, resulting in further climate impact from transport. In Scotland alone, 85% of the bricks used are imported. This greatly increases the carbon footprint of each brick.
Currently, every stage in the lifespan of the brick challenges the decarbonisation drive.
The amount of waste created by the construction industry presents a further environmental challenge. Across EU countries, the sector produces 800 million tonnes of waste each year, which needs to be repurposed and can no longer be sent to landfill.
Currently, every stage in the lifespan of the brick challenges the decarbonisation drive. Clearly, we must take a very different approach towards creating our built environment if we are to meet our net zero ambitions.
To urgently reduce carbon emissions in this sector, while extending the lifespan of our building materials, we must take a joined-up approach to construction, ensuring each aspect of the design and build process has as little impact on the environment as possible.
We must question how each element is made. What is it made from? Where does it come from? And can we make it more efficiently?
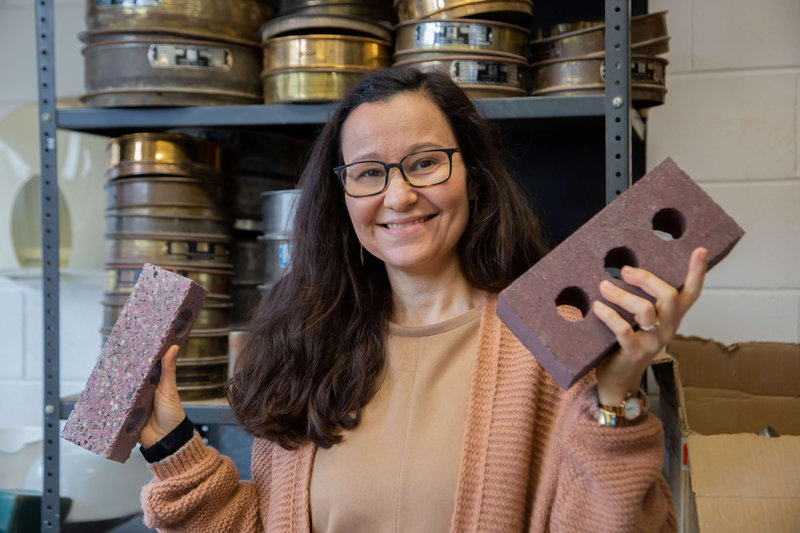
Gabriela Medero, co-founder of Kenoteq and professor of geotechnical and geoenvironmental engineering at Heriot-Watt University, with the K-Briq
Waste to walls: a new approach to manufacturing bricks
My team and I have spent over a decade trying to meet this challenge. We’ve worked with engineers, architects, chemists and geologists to develop an eco-friendly alternative to traditional bricks.
Ensuring circularity in the manufacturing process was important to us. We started at the end of the lifecycle of construction, examining the landfill created by the industry and researched how these precious materials could be given another life and purpose.
The K-Briq is made from 90% demolition and construction waste including concrete, rubble, old bricks and plasterboard. All ingredients are carefully put together without firing or cement addition. It can be made on a production line quickly, when compared to the traditional brick manufacturing process, which requires up to a week’s air drying followed by 10-40 hours in a kiln.
The manufacturing process uses less than a tenth of the energy used during the creation of a traditional fired clay brick and produces only a tenth of the CO2 emissions.
Within 24 hours of waste materials arriving at the processing facility from construction sites, the waste can be sorted, cleaned and made into K-Briqs ready for use.
Completing the circular economy pathway, Kenoteq manufactures onsite at a waste handling facility in Scotland to reduce transport miles and limit any additional CO2 involved in its production. Within 24 hours of waste materials arriving at the processing facility from construction sites, the waste can be sorted, cleaned and made into K-Briqs ready for use.
Prioritising faster and more efficient manufacturing processes will allow industry in the UK to manufacture more materials domestically and will reduce the need for expensive imports. We believe that by working with industry to better support brick makers to find new, more sustainable solutions, we can help evolve the industry as it strives to decarbonise.
We must also look to the future environmental impact of each new building we create when planning our built environment. Every effort must be made to ensure we are as energy efficient as possible and think strategically about the materials we choose to build with.
We need materials that naturally regulate building temperatures to minimise energy requirements once in use. We have ensured the K-Briq has a high thermal mass, which retains heat in the winter and keeps buildings cool in the warmer summer months, so heat and air conditioning costs and energy requirements are kept to a minimum.
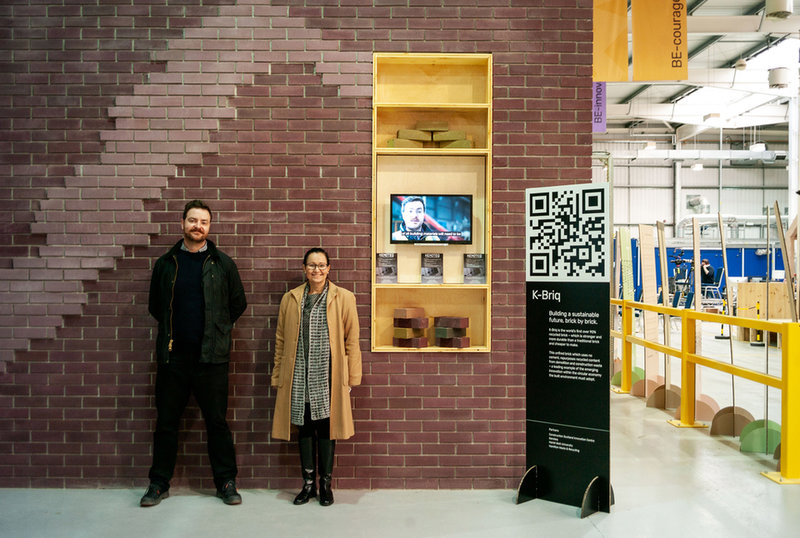
Kenoteq co-founders Professor Gabriela Medero and Dr Sam Chapman with a demonstration wall made of K-Briqs. Credit: Penny Black Co
Moving towards a circular model for materials
Decarbonising the built environment can’t happen overnight. There are many hurdles to overcome.
To allow the industry to adopt more innovative, low-carbon alternatives we need to see more support from government and changes in policy and legislation to support this significant step change in practices. Incentives to use and manufacture eco-friendly materials locally, combined with further research and development into new concepts and ideas, will help accelerate their introduction.
As COP26 has brought the challenges faced by the built environment to the forefront of public awareness, the time has never been better to start implementing these changes. We must see action on this, and fast.
Waste handling facilities around the UK can replicate this circular economy approach and reduce – or even remove – the need for imported construction materials.
We are developing the blueprint for how this can be achieved with brick manufacturing. Next year, we will be scaling production from our existing pilot plant to industrial-scale manufacture.
Waste handling facilities around the UK can replicate this circular economy approach and reduce – or even remove – the need for imported construction materials. This is a unique chance for the sector to make a significant contribution towards the UK’s net zero goals.
With governments around the world committing to placing the circular economy at the heart of their decarbonisation plans and paying increasing attention to the challenges presented by our built environment, increasing opportunities exist for planners, builders and architects to work with their clients to meet climate change targets.
By committing to building a greener world together, brick by brick, we will find our path to net zero.
Main image: The K-Briq. Credit: Zero Waste Scotland