Sustainability
The role of building design in net zero construction
Scott Wilson, head of sustainability at Black and White Engineering explains how modelling techniques used in building design must evolve to help reach net zero in the built environment.
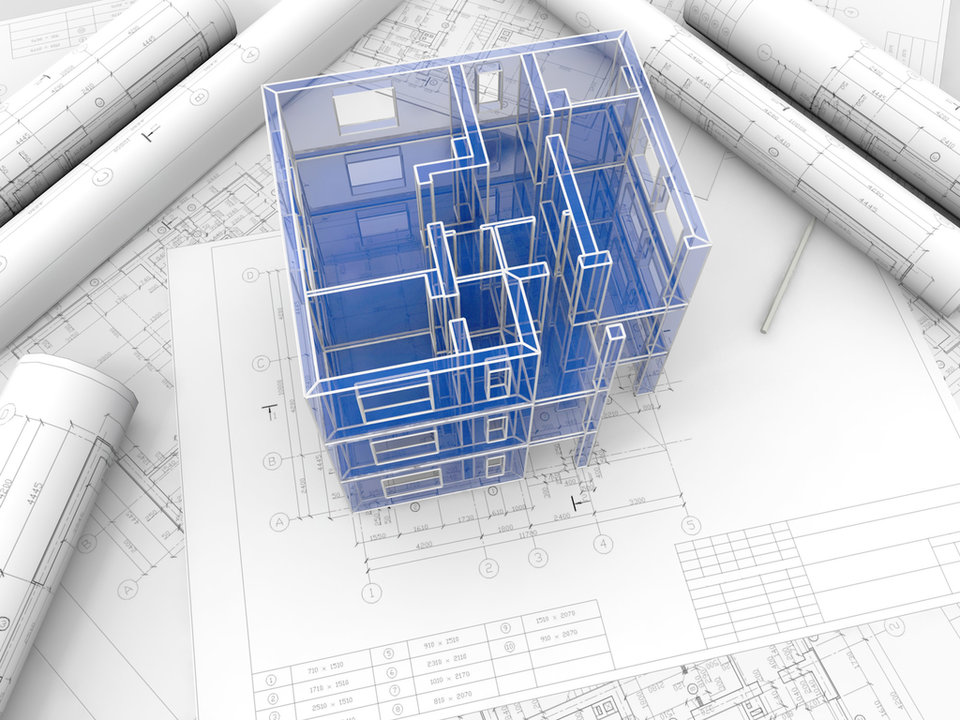
W
ith energy consumption from buildings contributing to approximately 30% of the UK’s total emissions, the pressure on the engineering and construction sector to design, create and build greener, cleaner buildings has never been greater.
Currently, the construction industry is using thermal modelling in line with Part L Building Regulations to assess the energy efficiency of a building. Under this approach, a building is considered to be net zero carbon where the net emissions arising from the energy consumed by fixed building services is less than or equal to zero. This is done by either meeting all site demands through renewable energy or generating enough renewable energy on or near site to offset the emissions from fixed building services.
This scope is limited as commercial buildings, such as offices, have significant small power loads that can be more than 50% of a building’s energy demand. Furthermore, renewable energy generation and the building’s energy demand may not coincide, resulting in times when the building must still require a conventional means of obtaining energy, such as through the national grid or fossil fuels. Part L is a design guideline only and no follow-up is required to ensure that the building is performing as predicted.
While this methodology serves to reduce carbon emissions, the scope of end uses covered is too narrow and it’s not an accurate prediction of a building’s energy consumption in use. The UK Green Building Council (UKGBC) methodology looks to remedy this by including all end uses within a building.
Furthermore, there is nothing within the building regulations to drive down embodied carbon. The embodied carbon can often be larger than a building’s emissions associated with operational energy and this is often not considered unless driven by local planning authorities.
Scott Wilson, head of sustainability at Black and White Engineering
Bea Sennewald, director of projects at Article 25
Predicted vs real energy consumption
The UKGBC’s framework addresses the gap between predicted energy consumption and actual energy consumption by basing claims of a net zero carbon building on real-life data from meter readings and utility bills. In doing so, this pushes the design team to work towards a much more accurate simulation at design stage so that options for reducing the energy demand can be tested and energy consumption can be minimised as much as possible.
As this is based on actual consumption data, claims of a net zero carbon building carry credibility and the industry is already seeing a significant uptake in designs targeting net zero carbon under the UKGBC’s framework.
By considering the embodied carbon, significant reductions in carbon emissions can be realised through the choice of materials, such as using a timber frame in place of a steel frame. By undertaking a detailed life cycle assessment early in the design, efforts can be focused on the elements with the highest embodied carbon, such as the superstructure.
Embodied carbon is assessed using a whole life cycle carbon assessment. Every material used in the building must be quantified and its associated carbon emissions determined.
When predicting any building’s energy demand, very detailed energy modelling is required. All plant performance parameters need to be taken into consideration, including part load efficiencies, to show how the building will operate under different conditions.
Stress test modelling must be included to take into account the unpredictable nature of building occupants, since the way the occupants use the building can have a significant effect on energy consumption. Once an energy model is built and a baseline has been determined, this can be used to decide the best strategy for the building.
Embodied carbon is assessed using a whole life cycle carbon assessment. Every material used in the building must be quantified and its associated carbon emissions determined. Where available, an environmental product declaration (EPD) for the product is used to determine its CO2 emissions per tonne or volume. If an EPD is not available, a software data base value can be used but this is considered to be less accurate.
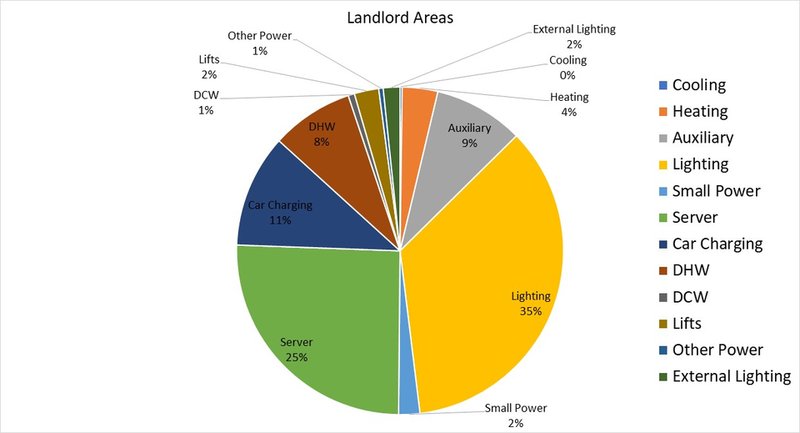
Breakdown of operational energy use in an energy efficient office.
Upskilling the workforce
The methodology required to predict operational energy modelling is not typically used in the UK or in the industry as a whole, which means workforces will need to upskill to use the tools required to run these models.
When designing a building, teams will need to think holistically and understand that there are trade-offs to be had between reducing operational energy and embodied carbon. For example, specification of triple glazing may reduce the building's heating demand but it will significantly increase the embodied carbon and may not be the best option.
A major obstacle to completing accurate life cycle assessments is the lack of manufacturers with EPDs. Many manufacturers do not currently have accredited EPDs and so the embodied carbon cannot be determined. In these instances, default database values must be used, but these can be very different from the performance of the actual products specified.
As the industry catches up, those manufacturers that have accredited EPDs are more likely to be specified, giving them a competitive advantage.
Main image: Grenfell Tower in West London, where a severe fire killed 72 people in June 2017. Photo by Andrew Redington | Getty Images