Materials
In harmony with nature: materials and interiors
Natural materials are set to become a trend driving design in 2021, an expression of the closer ties with nature many have formed during the pandemic and the ongoing lockdowns. With materials such as stone, wood, rattan and hemp set to become more popular, Alex Love takes a look at natural materials and furniture.
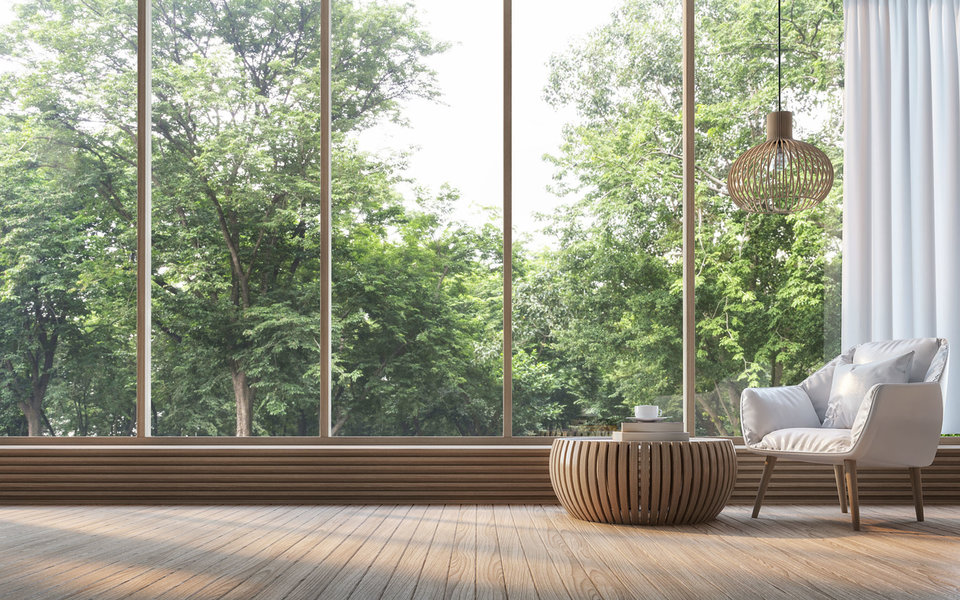
In
2011, the annual NBS BIM Report recorded BIM adoption at just 13%, with 43% unaware of the technology’s potential. Today, based on a survey of more than 1,000 industry professionals, some 73% of firms are now using BIM, while just 1% are unsure of what it offers.
While BIM has helped to improve communication and collaboration between stakeholders, there is still room for improvement. According to a recent survey conducted by the Institute of Civil Engineers and ALLPLAN, organisations face a variety of issues when using BIM, including unexpected design changes (55%), exchanging information between parties (45%), and incompatible software (43%).
These problems are, in part, caused by the wide range of software available – according to Newforma’s The State of Technology: AEC Firms report, there are seven BIM applications frequently used across thearchitecture, engineering, and construction (AEC) industry, and many more niche tools. While an architectural firm involved in a project may work in Revit, the structural engineer may prefer to use Tekla, and the mechanical, electrical and plumbing (MEP) engineers may use Navisworks, which causes issues to arise when sharing files.
Cob
Walls made from cob mass. Credit: Earthouse
Cob is an ancient building material that is experiencing a resurgence in an increasingly eco-conscious age. Made from chopped up straw, natural clay and sand, cob can be fashioned into bricks, blocks and larger elements to build walls.
This highly resistant material is capable of withstanding extreme weather, fire, and even earthquakes. Provided buildings are correctly maintained, structures built from cob can last for thousands of years. In fact, the oldest known cob house is thought to be some 10,000 years old.
While it is possible to make cob bricks at home, it is always best to consult the experts for larger projects. Devon-based Earthouse, for instance, is a specialist provider of cob building materials and services, carrying out restorations and repairs of old buildings.
Read more
Hempcrete
Walls made using hempcrete. Credit: Photograph copyright Alex Sparrow, UK Hempcrete
Hempcrete is a lightweight alternative to concrete, made by mixing chopped up hemp cores with a lime binder and water. To create walls, hempcrete is typically applied by spraying or plastering within shuttering to build up layers to support wooden framed buildings.
The material creates a solid wall that is airtight and thermally efficient. It has also been found to not shrink over time, minimising the chance of cracks appearing around timber frames. It is known for its insulation properties and ability to maintain a building’s internal temperature, which is unaffected by outside conditions.
Hempcrete can also be used for floors and roofs. This material can be made at home independently, but achieving the right consistency can prove difficult without proper training. UK Hempcrete is one provider of this type of building material and related construction services.
Read more
Mycelium insulation
Mycelium insulation panels. Credit: Biohm
British startup Biohm has discovered a means of essentially growing mushrooms that can be dried and turned into solid materials for insulation, dry cladding, interior architecture, and furniture. The process to create mycelium is described as carbon negative, as the fungus feeds on industrial waste such as cardboard, paper, timber, agricultural items, plywood and even plastic.
The material has been found to be highly resistant to fire. Biohm’s mycelium insulation panels are currently undergoing industry thermal and acoustic tests, with completion due for the third quarter of 2021.
The company has big plans for its bio-manufacturing facility, initially producing approximately 3,000m2 of insulation a month. The plan is to scale-up its facilities to have a monthly production capacity of 18,000m2 of insulation. This would provide enough insulation for around 120 homes, while consuming 180t of waste and removing 36t of carbon emissions.
Read more
Rattan
Rattan furniture. Credit: The Rattan Company
Rattan is the collective name given to as many as 600 species of climbing vines or palms found throughout the world’s tropical climates, notably in South East Asia. The material has many uses and is commonly weaved to make furniture and fittings.
Rattan grows seven times more quickly than trees and its lightweight properties offer a lower carbon footprint than timber when harvesting and transporting. It is a versatile material that is surprisingly durable. It is also fully recyclable and biodegradable, making it appealing for the circular economy.
The Rattan Company is a UK-based importer of rattan products made by rainforest communities, providing them with a source of income that helps to de-incentivise chopping down trees for palm oil plantation or agricultural use. The Rattan Company’s product range includes tables, chairs, light shades, headboard for beds, and cabinets.
Read more
Wood
The Wood For Good campaign encourages the use of wood as a building material. Credit: WoodForGood.com
Wood is another historic natural building material that is playing a key role in the sustainability drive. Known for its strength and multiple uses in construction, it is common across both building exteriors and interiors.
The timber industry’s campaign Wood For Good is promoting wood as an alternative to carbon-heavy construction materials such as steel and concrete. The group’s Wood CO2ts Less initiative aims to raise awareness of timber’s environmental benefits, highlighting that one of the easiest ways to cut carbon emissions is to use wood from sustainably managed forests.
Tree planting is also a big part of these plans. The group claims that carbon taken out of the atmosphere by trees is then locked away and effectively stored in wood used for products.
Read more
Grown natural furniture
Full Grown grows chairs from young tree branches. Credit: Full Grown.
Full Grown is a UK company that is literally growing chairs. The process involves pruning and encouraging young tree branches to grow over customised moulds to achieve specific shapes.
Branches are carefully grafted together to create a solid object. Once the structure is in the desired shape, it is tended to while it matures and becomes thicker. It is harvested during the winter months and dried out for the necessary time, with planing and finishing then performed.
The company estimates that the process consumes 25% of the energy used to manufacture a wooden chair by conventional methods. It can take around four to eight years for a Full Grown chair to become the finished product, and customers also face a waiting list.
While it’s hardly an item you can order expecting next-day delivery, it is a unique piece of furniture made almost entirely by nature.
Read more
Stone
Stone is a robust and lasting flooring material. Credit: Stamford Stone
The oldest building material is surprisingly versatile, with uses that include walls, fixtures, flooring, and cladding. The material can vary greatly depending on where it is sourced, with sandstone, limestone, granite, and flagstone abundant in different areas.
Stone can offer a means of lower carbon construction than other materials, provided it is not imported from thousands of miles away, offsetting heavy emissions from transportation. And because natural stone is mostly used in the state it is dug out of the ground, it does not require carbon-intensive processes such as ovens or kilns. It only needs cutting, shaping or finishing for its intended purpose.
Limestone flooring, for instance, is a robust and long-lasting product that fits the design of most kitchens or living space. Stamford Stone not only provides finished products such as this, but also owns quarries in Lincolnshire where it sources many of its building materials.
Read more
Main image: The Kinder Building in Houston features a façade made of translucent glass tubes. Credit: Richard Barnes / Steven Holl Architects